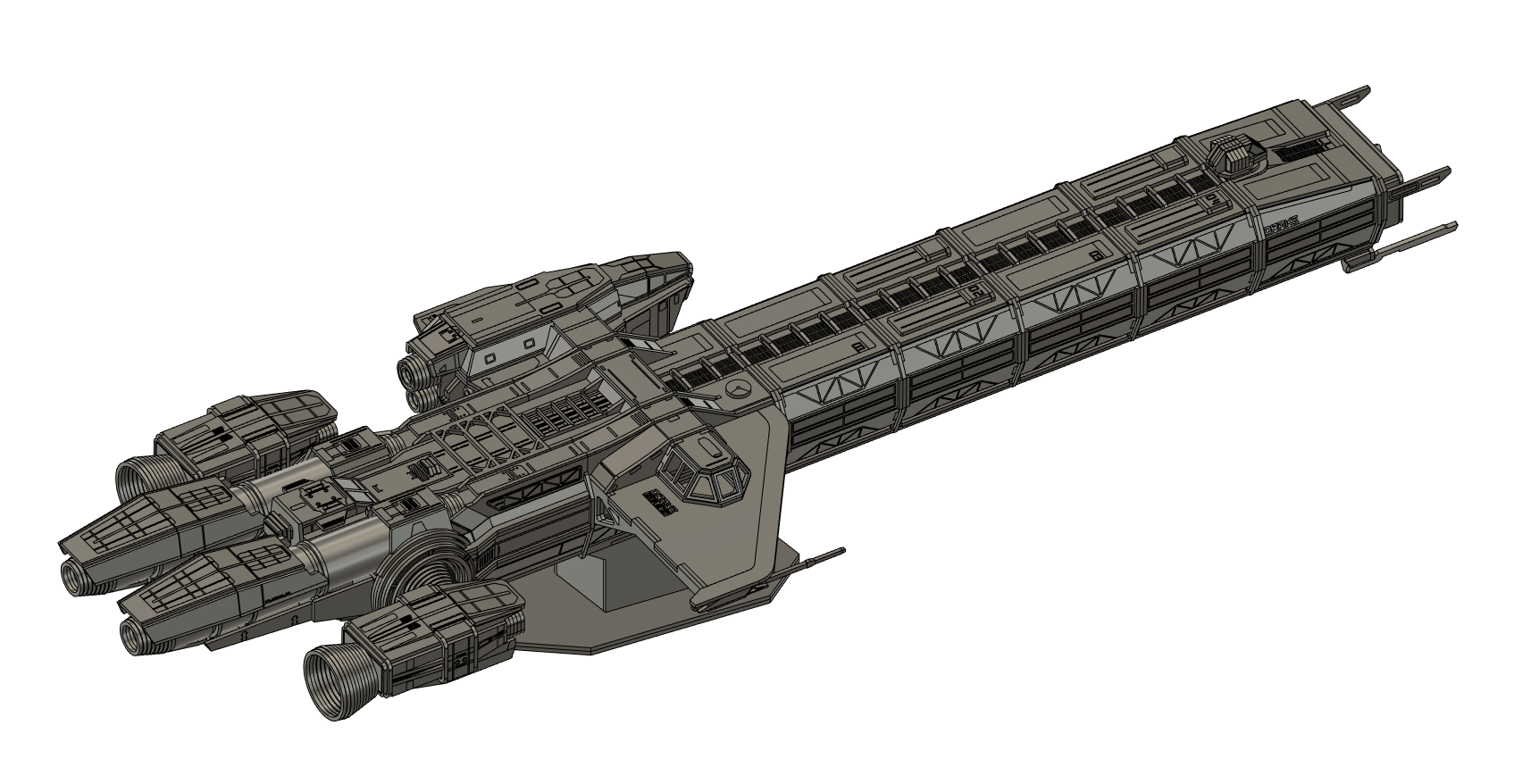
Star Citizen Drake Caterpillar 1:100
A downloadable model
Hey there!
If you are only here to download the files, jump down to the section where it says "Tipps on cut-out and assembly". If, however, you are interested in me telling you about how Ive made this model and the story behind it, read the following, hope you enjoy:
Story and Background
The Drake Caterpillar holds a special place in my heart for a few reasons.
When i started playing SC in alpha 3.9 it was the first big ship that i got to fly as part of a multi crew drug run organised by a small streamer at the time.
As i was a very unskilled pilot at the time, i had a quite real fear and respect for it and saw it more of a thing i need to cooperate with then something that i command.
Over my years playing star citizen, that fear and respect turned into a great joy of flying big heavy ships and the Caterpillar remains my favourite big ship in the game till this day.
Apart from Star citizen, in my free time I do a lot of 3d modelling and laser cutting with fusion 360, thanks to their student license i have had completely free access to their software for many years now which is amazing, especially if the alternatives are adobe-like models that simply are not affordable for a student.
In the past I've done a number of projects for myself and did a bit of freelancing as well when i found the time for it.
Eventually i wanted to make a model of a star citizen ship, and I chose the anvil arrow as a small project to try my hands on. The arrow was relatively easily done, with a reasonably simple shape and a design that didn't have any complex curves in it I was confident i would manage, and so i did.
After that project was done i was ready to move on to bigger things, and so i decided to make a model of one of my favourite medium sized ships, the Anvil Valkyrie.
In the beginning it went well, however the more the ship developed, the weirder the parts had to be to fit the form of the ship and eventually the model looked like low poly version of the original and i scrapped the project.
For those that are not familiar with the laser cutting process, a laser cutter can cut most things except metal and stone as long as they aren't too thick, i work mostly with 3mm thick mdf or hdf as they are easy to cut and have a consistent thickness even across big plates. This cutting out of plates however makes realizing bends or curves extremely difficult. Not impossible but only if the radius is not too tight and the bends can only be along one axis.
So the Valkyrie was a bust and i set the idea aside for a bit until i realized that the Caterpillar would make a good candidate for a model. Drakes industrial design and the caterpillars distinct boxy form would work perfectly with the constraints that come with laser cutting.
Motivated, i got to work on a 1:250 model of the caterpillar, but soon i found out that the scale was too small to capture any detail to my satisfaction so i abandoned that first attempt.
Some time later i started again, this time with a scale of 1:100. Again, it went well at first and i got the cargo bays worked out quite fast as they are an easy shape and can be copied over to make a large part of the ship. But again, after some time, I lost the motivation for the project and abandoned it again. That was almost exactly a year ago.
At the time, the Caterpillar wasn't the biggest project I've ever made. I once got commissioned to do a scaled model of a real live castle. The model was about 1m in length and me still being unexperienced with time management at the time accepted the job expecting it to take 2-3 weeks max...
It ended up taking 3 Months, but since i got payed for it and it was for someone else and they were expecting things, I powered through it. And as a reward for myself and because it was my biggest project, i build it for myself as well and ever since then, it has decorated my room as my biggest masterpiece ever.
Back in September 2023 i started getting tired of castles sight. I liked how it turned out, but I am not the type to put a castle in my room for decoration.
So my mind wandered to the things i could put there instead and i remembered the Caterpillar.
With this new found motivation, i started the third version of this project. And somehow that motivation persisted because i have now completed it and it is sitting on that place where the castle was in this very moment.
The Design
This is the part where i nerd out about the design of the caterpillar and how I tried to capture its design into the model.
First of all, the references I used.
There is an amazing sales brochure that CIG published alongside the Caterpillar (https://robertsspaceindustries.com/media/2lxuyk90h9qupr/source/Carterpillar_brochure.pdf) Its a 28 page long Document filled with litte details, pictures, descriptions of function and most importantly, blueprints.
Those blueprints where the underlying guides i used to get the dimensions and proportions right when designing the hull.
Another massive help were the isometric pictures from the star citizen tools website (https://starcitizen.tools/Caterpillar) having pictures that show the design of the caterpillar from all angles proved to be essential when doing the details on the hull.
And here I also have to give huge props to Autodesk for making an incredibly solid piece of software.
I really was not kind to fusion 360. All 900 bodies were in the same component for the longest time, there was no order, i had parts cross referencing each other all over the place and the timeline is just way too long to comprehend. And while fusion 360 slowed down significantly towards the end of the project, it never crashed once in all the 4 months I've worked on it. And that all, from a student licence 100% for free for years now.
In times where Adobe ramps up its pricing for its subscription where even the student version costs 60 bucks a month and nearly every other industry giant does it alike, giving students access to a powerful 3d software for free is incredible.
(I don't say that they never done something wrong or are entirely the good guy, just in case they did something bad, don't cancel me please thank you)
Now for the cutting part:
You see, making stuff with a laser cutter and out of wood, it has a very distinct look that i always liked, but that is also quite challenging to incorporate with other designs sometimes.
For example:
- The model will be blocky and have a lot of edges
- If you dont want to paint, you have two colours. The colour of the wood and the colour of the burned edges, you can leverage this effect to a great extend if you know how, but you must be deliberate in where to separate pieces and where to put edges in order to make it pop
- An example for this are the cargo modules. They are separated by pieces that have their edges visible from the outside which gives the cargo modules a very clear separation
- If you want to have slight bends, it comes at the cost of that area being very dark and charred because you make a flat thing bendable with a lot of specific cuts
- You can add details to a surface by engraving stuff into it, however you can only engrave from one side. You could cut the part, engrave one side then flip it and engrave the other side but that makes the cutting process exponentially more difficult
Keep all that and a few more things in mind and you can leverage the design effects that come with laser cutting to a great extend.
The cargo modules
I've already talked about the cargo modules and how i visually separated them by having the burned edges of the walls be visible from the outside.
But another feature i wanted the cargo modules to have is that you can open them and look inside. This proved to be quite challenging because i would sacrifice a lot of stability for looks but i did manage to make it work.
The doors are hinged on parts that align with pockets in wall and have a 2mm hole where a toothpick can slot through them to the other side, and the doors are a slight press fit with the walls so that they stay shut when closed. Inside, the walls have a bit of engraving in them that hint at the hydraulics that the cat has in the walls to make the gates move.
Ive also managed to integrate the continues catwalk that runs through the cargo modules complete with ceiling mounts and ladders.
And in the floor Ive carved a grid of holes about 1mm deep and 1.25 cm apart.
Now what is 1.25m (remember 1:100 scale) in length? Exactly, an 1 SCU box.
So if you were to design a 1.25x1.25x1.25 box with 1mm tall feet at the bottom, you can stack cargo in the caterpillar like you would be able to ingame. The cargo bays 1-4 are accessible and should have the correct amount of cargo space to the real ingame Caterpillar. However i still have to design those SCU boxes 1.25 cm is a bit small to make so i will probably go with a bunch of 8 SCU cargo boxes and stack those in there.
The front cargo module is not accessible as i was not able to figure out a mechanism that would let me the front door seamlessly, it does have an interior though, although be it without detail.
The command module
The command module was the first truly challenging part about this model as it had slight curves to most of its edges and also i had to eyeball many of the proportions since the blueprints were insufficient. It took me a long time to get this part right and I've done multiple alterations of parts of it to get it satisfactory.
The side wing
The side wing was probably the easiest part of the whole model, simple shape, clear outlines in the blueprints, very straight forward
The side engines
The side engines are very round and i did struggle alot to get the shape where i am happy with it. In the end a mix of having a box with multiple layers that hide the boxiness and a large stack of circular cut-outs as the engine exit did the trick. And while i would like them to be less boxy i do think they capture the visual of the in game version quite well. The side engines are amongst the trickiest parts to assemble as it has a lot of parts that look alike but arent and also because many pieces only share an edge for gluing and not a surface.
The rear part of the ship
The rear part of the ship that houses the components, the living section and most of the hallways in game were both easy and difficult at the same time.
The outside design is not too difficult as it just continues the straight lines established by the cargo modules. The inside however was a different story.
I decided not to put any interior in here as it wouldnt be worth the traid off for stability. This was the point i wanted the whole model to blance on so it had to be super rigid.
It turned out quite rigid enough but getting there without having parts that couldn't be assembled because they would interlock somehow was difficult and there is a not immediately obvious way to assemble these pieces without it being more difficult then it has to be.
Also in here are 4 gears that interlock and go out left and right to the side engines. The idea was to have the side engines being able to pivot similar to how the Cutlass Black can, but i found that wooden gears with that much weight attach have too big of a backlash an the engines sack alot as a result. Still i left the mechanism in the download files just in case.
The main engines
I left the main engines for last in the design process as i wasnt sure how to make the round tubes that are a big portion of them, i did not want to stack endless amounts of circular cut outs as it would be not only tedious but also wouldnt look nice. In the end i settled on cardboard boxes i cut strips out and if you set the laser to cut through the top layer but not the bottom layer of the cardboard, it can easily be folder at that point and with a series of parallel cuts about 1cm apart a cylinder is easily made.
The main engines are also the most fragile part of the whole build precisely because of the cardboard cylinders as they can easily crumble when held on to.
Tipps on cut-out and assembly
Should you want to assemble this model yourself, a fair warning:
This is essentially a 900+ 3D puzzle with no instruction manual and no user friendly assembly being kept in mind during the process.
Parts range from 26 cm to less then 1 cm in length. Some parts will look like the they are leftovers from other parts while actually being used at some point so don't throw away any of the pieces until you are 100% sure you don't need them or else you will have to remake them.
You will need the fusion 360 file as a reference to see where parts belong.
For ease of use i have grouped the parts in selection groups that correspond to the groups found in the files. I will try to convert the file to a more generic 3d file format so that it can be viewed with other software as well, there i cannot guarantee for the grouping to be the same though.
In the .svg files, there are 3 colors.
- Red is meant for cutting
- Blue is meant for marking (like cutting but not through the material)
- Green is for engraving the area (engraving essentially 'fills' the area similar to a paint bucket with the difference that it removes material) The resulting area should be indented by about 1mm
My settings for the laser (80W machine) when cutting 3mm hdf are:
- cutting: 35mm/s speed, 65% power, 2 passes
- marking: 60mm/s, 25% power, 1 pass
- engraving: 100mm/s, 25% power, 1 pass
The model is meant for 3mm material, anything else wont work unless you want to do some heavy remodelling.
In my experience, you don't want your parts to dry fit. When the laser cuts, it burns a slight v-shape into the part so your edge will not be a perfect 90°, pressing the parts into each other will make them be at the same angle difference and results in non right corners where they should be which over time adds up and brings the entire model out of alignment. Besides to have the model be able to hold itself up, you will need to glue every part on anyway, i learned that the hard way.
For cutting rounds you will have to find your own way of doing that as the success varies from material to material, online you can find alot of templates for this.
For the tubes at the rear engines i would reccomend using cardboard from cardboard boxes but you may use whatever works for you of course
Download and license
Well then if i didnt scare you off with the previous section, then you are now free to download the files.
I decided to provide the files for free to the community because why not.
You can set your own price if you want and that would of course be appreciated but you dont have to.
Just note this:
- Dont abuse this free gesture and claim ownership of any of the content you download
- You are allowed to make changes to the model however you want
- Should you post photos of the model, modified or not, please mention me by my handle @justAnotherAnotherUser or @Proprogramer, or you tag my instagram https://www.instagram.com/pr0pr0gramer/
- by downloading the files, you agree to the above mentioned terms
Status | Released |
Author | justAnotherAnotherUser |
Genre | Puzzle |
Tags | 3D, lasercut, Modeling, star-citizen |
Download
Click download now to get access to the following files:
Leave a comment
Log in with itch.io to leave a comment.